It has to do with propshaft (aka "driveshaft") critical speed.
What you guys might be missing is that propshaft critical speed not just based on wheelbase but is also based on trans type (length), rear axle ratio, tire size, and engine type (larger engines allowing a higher top speed) AND/OR any strange resonances in that particular combination (camping out on that resonance will break the trans/transfer case tailshaft housing).
So - a long wheelbase truck with a low (numerical) rear axle ratio spins the shaft slower and might get a one piece, but an otherwise comparable truck with a high rear axle ratio might get a two piece.
One other comment - critical speed is not directly related to balance, but rigidity. When the shaft exceeds it's critical speed it begins to bow in the middle and swing like a jump rope. Hence the disturbance and durability concerns.
You can get around it by going to a larger diameter steel tube - or more expensive alternative materials like aluminum, carbon fiber or "metal matrix" (an aluminum/carbon wrap).
So - on the two 350 trucks - there could have been a tire difference that put it over the edge, or perhaps a different horsepower rating which would allow for a higher top speed. I can assure you there was something different there that is not obvious to us after the fact.
By the way, I hate the complexity and mass of a two piece setup and go out of my way to order my trucks such that they get a one piece shaft.
K
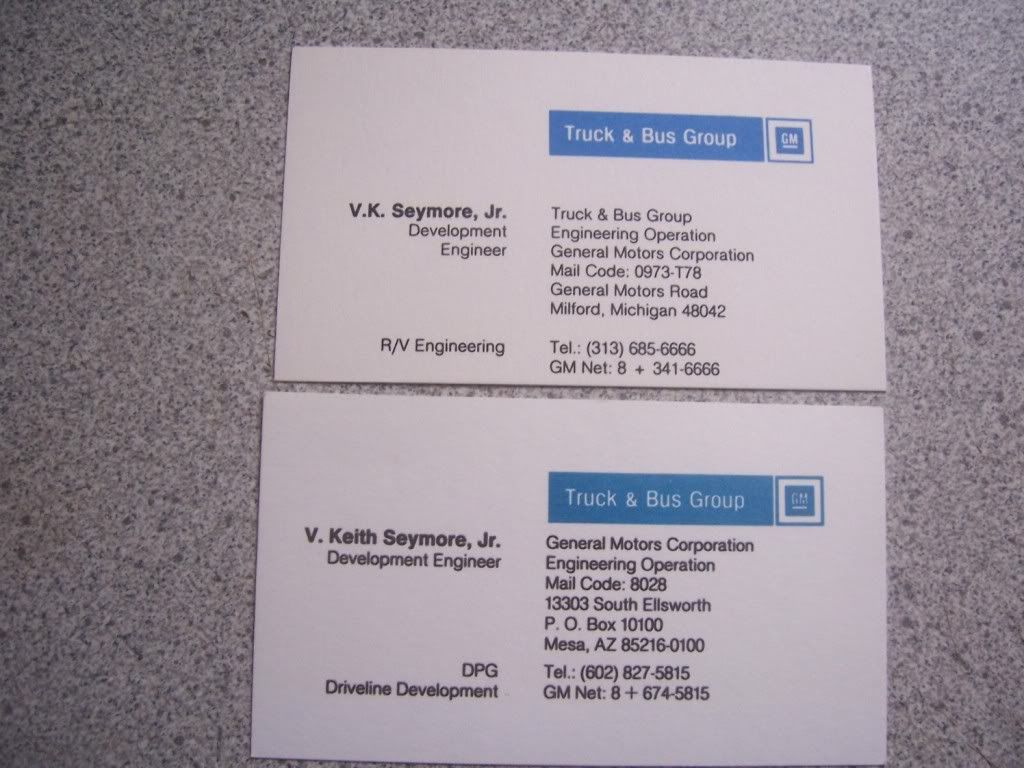